Type A Roof Deck
A DECK (NARROW RIB)
STEEL ROOF DECKING DIMENSIONS & INFO
PRODUCT INFO
Industry Designations
Type A
Narrow Rib
NR
Type A roof deck is the “original” term for this deck profile, though recently the Steel Deck Institute has promoted the more descriptive name, “Narrow Rib Roof Deck”, or “Type NR”.
Finishes
Prime Painted
Galvanized
The most economical finish for commercial metal roof decking, specifically Type A metal roof deck, is prime painted grey over bare steel, rather than galvanized painted . Typically, this finish provides adequate temporary protection to the base metal during construction. Additionally, prime finishes should indefinitely protect the base steel if it is in a properly enclosed, dry interior environment.
In cases of more aggressive environments – or a necessity of greater corrosion protection during construction – a galvanized coating in either G60 (0.6 ounces of zinc per square foot of metal) or G90 (0.9 ounces of zinc) is recommended. A G90 galvanized finish is typically required in government projects.
When trying to avoid field paint adhesion issues when using galvanized metal roof deck, it is recommended that you use a galvanized and prime painted finish when galvanized deck is to be field painted.
A white primer is also available for the underside of the A roof deck. However, this requires a longer lead time and could take up to 12 weeks. If a field coat of paint is not going to be applied, great care must be taken to protect the Type A roof deck from moisture before it is installed and covered in a dry environment. This is the same for all white-bottom roof decks. If the design requires a white bottom finish to be left exposed, the best finish to use is galvanized (G30 or heavier) and painted white.
Gauges
22
20
18
Type A roof deck is most readily available with material thicknesses defined by the even gauges 16, 18, 20, and 22. These correspond to design thicknesses of 0.0598”, 0.0474”, 0.0358”, and 0.0295”, respectively. While metal decking can be produced in any material thickness between 16 and 22, defining an “odd” or “special” gauge will make the deck much more difficult to source.
No. of Spans | Deck Type | Max Const. Span |
1 | A22
A20 A18 |
3'-9"
4'-8" 6'-0" |
2 or more | A22
A20 A18 |
4'-7"
5'-3" 6'-0" |
What is a Type A Roof Deck?
Unlike other types of metal roof decking, Type A roof deck is rarely used for new construction projects but is often needed for repair and re-roof projects. Type A decking is the least efficient 1.5” deep steel roof deck section. Type A metal roof decks have the lowest strength-to-weight ratio compared to Type B and Type F. As with all steel products, the lighter the steel deck section, the more economical it will be. And since the Type A roof deck cannot carry as much load at longer spans as B and F decks, the steel supports below the metal deck must be spaced closer together. In turn, a smaller support spacing results in more support and higher costs for the building owner.
To illustrate the significant disparity in capacities, consider the Factory Mutual maximum deck spans. For 22 GA 1.5 A Deck, the maximum span is only 4’-10”, but the maximum span increases to 4’-11” for 22GA 1.5 F Deck and 6’-0” for 22GA 1.5 B Deck. The Maximum Construction spans published by the Steel Deck Institute for two or more spans show a similar pattern. These maximums are 3’-9”, 5’-3”, and 6’-11” for Type A, Type F, and Type B, respectively.
When other types of metal roof decking, such as Type A and Type F were developed, the strength of the metal deck was only one factor that the engineering community was concerned with, and it was secondary. The primary objective was to maximize the width of the top flange to provide the maximum amount of support for the roofing insulation that would be installed on top of it. Over time, roofing materials improved, and steel deck manufacturers could reduce the width of the top flange, increasing the efficiency of the steel deck section from Type A to Type F decks and finally from Type F to Type B decks.
Load Capacity Limitations
Type A metal roof decks have a lower load capacity than Type F and Type B because the top flange of the metal deck is in compression. When thin metals like 22 gauge or 20 gauge (.0295” and .0358” thick, respectively) are compressed, it is much more difficult to predict how and when they will buckle when compared to thicker sections of 0.5 inches or more. However, it is easily demonstrated that bending thin metals strengthens it significantly. While the moment of inertia of the bends can be reliably calculated, the moment of inertia of the thin, flat compression flanges is more complex. The material closest to the bends will resist buckling better than the flat material positioned further away. Since Type A has the largest top flange (5” versus 4.25” for the F deck and 3.5” for the B deck), a large part of the top flange is not considered effective in resisting the compressive forces that result from bending. To overcome the larger amount of ineffective material in the flat top flange, deck manufacturers added a minor rib, or “stiffening rib,” to the top flange of the Type A narrow rib roof deck. This increased the capacity of Type A roof decks. Still, Factory Mutual researchers were concerned that the adhesives used for installing roofing insulation would accumulate in the stiffening ribs and create a fire hazard. As a result, deck manufacturers had to either remove the stiffening rib and produce a weaker section that would be approved by Factory Mutual or manufacture a stronger section that could not be “FM Approved.” Since Type B roof deck is lighter and stronger than Type A roof deck and, therefore, more commonly used, most manufacturers chose to produce a roof deck that would be FM-approved.
Replacement or Reapplication
Replacing a Type A metal roof deck in a repair or re-roof application may present some challenges compared to replacing a Type B deck. Since the existing narrow rib-type roof deck may have a stiffening rib in the top flange, the supports may be spaced further apart than the “modern” Type A narrow rib roof deck, which can span at the same gauge. For example, a roof that was constructed in the 1970s may have supports at 5’-0” on center with a 22 gauge Type A roof deck. If a new deck is to be installed on this roof, it will need to be 20 gauge since the maximum span for 22 gauge is only 4’-7”.
When using a Type A roof deck to cover skylights, note that a 20 gauge deck or heavier will probably be required since 22 gauge will only span 3’-9” (see maximum unshored spans for one (1) span). As shown in the Maximum Construction Span table on this page, the maximum span for one span is 10 inches shorter than the maximum allowed when each deck sheet covers two or more spans.
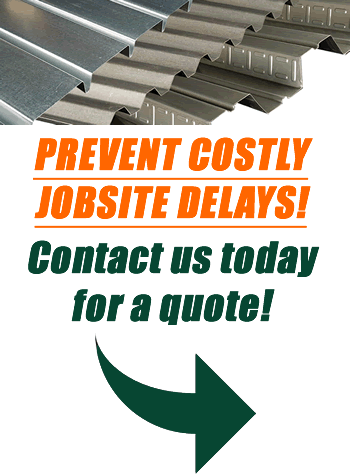
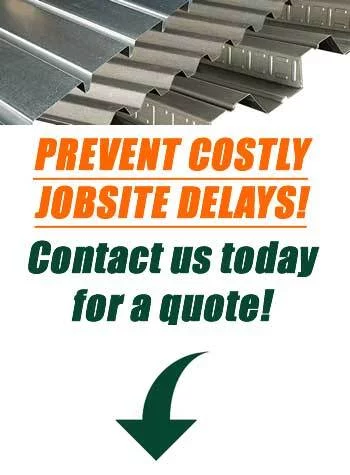
"*" indicates required fields